3000tpd cement production line
The Pengfei EPC cement production line project includes services such as process design, equipment supply (including mechanical and electrical parts), civil engineering, installation and commissioning, trial operation, reaching production standards, and final delivery. Mechanical equipments include limestone crushing and conveying, clay crushing, and auxiliary raw material pre-homogenization yard, raw material batching station, raw material grinding and waste gas treatment, raw material homogenizing warehouse and raw material entering kiln and firing kiln Tail, firing kiln and tertiary air duct, firing kiln head, clinker transportation, clinker.
Introduction
The Pengfei EPC cement production line project includes services such as process design, equipment supply (including mechanical and electrical parts), civil engineering, installation and commissioning, trial operation, reaching production standards, and final delivery. Mechanical equipments include limestone crushing and conveying, clay crushing, and auxiliary raw material pre-homogenization yard, raw material batching station, raw material grinding and waste gas treatment, raw material homogenizing warehouse and raw material entering kiln and firing kiln Tail, firing kiln and tertiary air duct, firing kiln head, clinker transportation, clinker storage and transportation, cement batching station and clinker bulk, gypsum, crushing and transportation of mixed materials, cement grinding and transportation, cement storage And transportation, cement packaging, bagged cement loading, cement automobile bulk, machine repair workshop and sum material warehouse.Process parameters
(1) Clinker output: ≥3000 t / d; (2) Heat consumption for clinker burning (3) Comprehensive power consumption for clinker (4) Comprehensive power consumption for cement (5) 28-day intensity of clinker (6) Dust emission concentrationProduction method
Cement production uses limestone and clay as the main raw materials. After crushing and batching, raw materials are produced. The raw materials are fed into a cement rotary kiln for calcination. Then, the clinker is added with an appropriate amount of gypsum, mixed with some mixed materials or additives, and ground by cement It is ground into cement and then shipped by a packaging machine or bulk machine. Cement production equipment usually uses the dry cement production process. A method for simultaneously drying raw materials and grinding them into raw meal powder and feeding them into a dry rotary kiln for calcination of mature materials. The main advantage of dry production is low heat consumption. |
Process flow description
5.1 Limestone crusherA limestone crushing plant is installed at the plant . Quarried limestone is dumped by trucks into dump hopper made of concrete and lined with steel plate with bars and extracted by means of a heavy duty apron feeder with a capacity of 550 t/h to crusher.
The crusher is of hammer crusher having a capacity of 550 t/h. It is capable of crushing limestone lumps with a maximum size of 1,000 mm edge to edge to a size less than 75 mm. To prevent the crusher from overload, the apron feeder speed is changed by a hydraulic drive unit in response to the power consumption of the crusher drive motor. A scraper conveyor is equipped so that spilled material from the apron feeder is collected on it. Crushed limestone is transported by belt conveyors to circular pre-blending bed. Belt weigher with a totalizer is provided for measurement of a crushing capacity. A pulse jet scavenging type bag filter is provided for dedusting of the crushing plant.
5.2 Limestone pre-homogenizationCrushed limestone is stacked of a lateral boom type having a capacity of 600 t/h to circular stockpile of 24,000 tons. A bridge type reclaimer with a capacity of 300 t/h is provided for extracting the limestone onto a subsequent belt conveyor
5.3 Auxiliary materials and coal crushing and transportationThe corrective (Clay, Iron ore, and etc.) and coal will be transported into plant by dump truck .The crusher will be fixed in covered stockpile. An apron feeder will feed the materials with less than 10 moisture content into a crusher. The crushed materials will be transported with a belt conveyor to long pre-blending stack yard.
5.4 Corrective and coal preblending Corrective are dumped by trucks into dump hopper made of concrete and lined with steel plate with bars and extracted by means of a heavy duty apron feeder to crusher.
Crushed materials will be stored in longitudinal material preblending bed. Belt Weigher with a totalizer is provided for measurement of a crushing capacity.
Coal is conveyed to preblending storage with belt conveyor. These material is stacked by a lateral boom type, form two longitudinal stockpiles. Two cantilever type reclaimer is provided for extracting Corrective material onto a subsequent belt conveyor to raw material proportion hopper and coal hopper.
5.5 Raw material proportioning and conveyingThe raw material proportioning station has 4 bins: the limestone bin, the mixture bin ,the clay bin, iron bin. Under each bin, a weighing feeder discharges the material from the bin automatically and smoothly according to given proportioning ratio. The mixed raw material is transported to the mill by a belt conveyor.
5.6 Raw material grinding and waste gas treatment A vertical mill will be used for raw materials grinding. The capacity of the raw mill is 210t/h. The raw materials will be proportioned according to the set ratio before they are fed to the mill for grinding and drying. The ground material will be carried by air to the cyclone separator and the coarse particle will be collected by the integrated separator and returned to mill for regrinding. The dust laden air out of the cyclone separator will be treated in an bag filter before being emitted into the atmosphere (<30mg/Nm3). The raw meal collected by the cyclone separator and the bag filter will be sent to the raw meal homogenizing silo. The hot air for drying the raw material will be drawn from the cyclone preheater.
5.7 Raw meal homogenizing silo
The blending system comprises multi-feeding systems and a continuous blending silo with a capacity of 7,500tons. The multi-feeding system ensures to build up uniform layers over the entire cross-section of the silo. Homogenizing action is effected by funnel flow during discharging process activated by cyclic aeration in the bottom zone. This blending system shows high homogenizing efficiency with low energy consumption. Homogenized raw meal is sent to kiln feeding system in the bottom space of the blending silo.
The homogenized raw meal is metered by electric flow valve and belt weigh feeder, after which it is sent by conveying equipment and bucket elevator to the up-stream duct of the preheater. The air for homogenization silo should be supplied by roots blowers.
5.8 Kiln feeding system
The raw meal from the raw meal homogenizing silo is sent to a weighing bin. After being metered by an impact flow meter under the bin, the raw meal is sent to the preheater system by a belt type bucket elevator. When the kiln is stopped temporarily, the raw meal is returned to the raw meal homogenizing silo.
5.9 Clinker sintering system
Φ4.0x60m dry process rotary kiln with single series 5 stages cyclone preheater and precalciner as well as grate cooler will be used. The system capacity is2,500t/d and the heat consumption 740 kcal/kg. The raw meal will be weighed before fed into preheater for preheating and partial de-carbonation and then into precalciner for calcination. The de-carbonation rate of CaCO3 in the raw meal at the kiln inlet is about 95%. The raw meal is further de-carbonated and burned in the kiln. The clinker which temperature over 1,350℃ will enter into the grate cooler for quenching. The clinker temperature at the outlet of the cooler will be 65℃ plus the ambient temperature.
The exhaust gas out of the preheater which temperature about 310℃ will be used for drying the raw materials. The exhaust gas out of the cooler will be introduced into the bag filter for purification before being emitted.
5.10 Clinker storage
From the cooler, clinker is discharged onto clinker bucket chain conveyor and transported to a clinker silo of 27,000 tonne. A underburnt clinker bin with capacity of 500 tons will be set up at inside of the silo. Clinker will be transported to the clinker proportioning bin by belt conveyors.
5.11 Gypsum and additive material crushing and conveying
Trucked to the site from the its mine, gypsum directly discharged at an exclusive tipple, and crushed in the PEX250×1000 crusher.When the crusher is off, gypsum is kept in exclusive pile, later sent to crushing tipple by frontloader. After crushing, the gypsum then be sent to the batch silo by belt conveyors.
5.12 Cement grinding
Clinker, gypsum, limestone or other additive are extracted from respective hopper by means of weigh feeders equipped with a speed controller in proportion to a predetermined rate.
Two units of φ3.8×13m ball mills are the main equipment in the cement grinding department. The weighing feeders under the bins will feed the materials according to the setting ratio. The mixture will be fed to the mill by the belt conveyor. The ground cement material will be sent to the separator by the bucket elevator and air slide. The finished product will be sent by the air slide to the cement silos and the coarse particle will return to the ball mill. The exhaust gas out of the mill will be purified in the bag filter and emitted into the atmosphere.
5.13 Cement storage
Four cement silos with diameter of 15m, and storage capacity 20,000t. The cement from the cement mill transported to the top of silo by elevator. The cement in the silo passed slide to middle bin, cement discharged from middle bin was transported from cement bulk vehicle (3×150 t/h), another transported to the cement packer by air slide.
5.14 Cement packing
Two sets of cement packer (8-spout rotary packer, 100t/h) will be used for cement packing.
The dust caused by packing is collected by bag filters and sent to bucket elevator before the packer by screw conveyor while the waste air drained through a fan.
5.15 Coal grinding
Coal grinding system will adopt ball mill. When raw coal moisture is ≤10%, product moisture is ≤1%, and raw coal size is ≤25mm, product fineness is 80m sieve residue ≤10%, and then the output of the whole system is 18t/h.
5.16 CCR and central lab. In the CCR, the routine process operation and control will be executed, and in the central lab, the quality control and test of raw material, fuel, finished product and semi-finished product will be carried out.
5.17 Air compressor station
An air compressor station will be installed, 5 sets of screw air-boosting compressor in all of 23m3/min as displacement and the pressure is 0.8Mpa,furnishing the dry, oil free and water free compressed air for consumers in the production line.
Technica
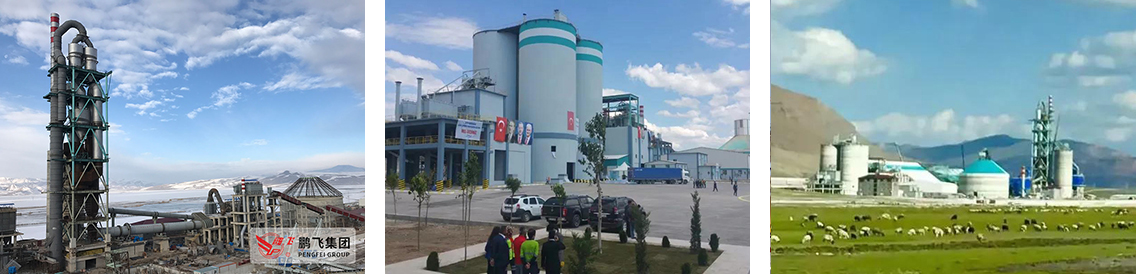
No. | Department | Technical performance | Capacity(t/h) | Qty | Annual running Rate(%) |
1 | Limestone crushing | heavy duty plate feeder size:B2000×9018mm grain size: ≤1000mm power:45kW(V·F) |
550 | 1 | 17.6 |
single-stage hammer crusher size:PPC-2018 product size: ≤65mm(90%) power:710 kW |
550 | 1 | 17.6 | ||
2 | Limestone pre-blending storage | Side cantilever stacker Material repose angle: 38° Capacity:500t/h scraper reclaimer Capacity:300 t/h power:~125kW |
600 300 | 1 1 | 17.6 32 |
3 | Clay crushing | clay crusher maximum size:<400mm Discharge size (residue10%): ≤50mm material moisture:≤20% power: 2×37kW |
80 | 1 | 20 |
4 | auxiliary materail and coal pre-blending | Side cantilever stacker Material repose angle: 38° Capacity:250t/h scraper re-claimer Capacity:150 t/h power:~125kW |
250 150 | 1 2 | 19 32 |
4 | Raw mill | Vertical mill feed moisture:≤10% feed grain size:≤75mm discharge moisture:≤1% discharge fineness: ≤14%(0.09mm residue) motor power: 2000kW |
210 | 1 | 70 |
Separator Type: motor power:110kW |
1 | 70 | |||
Circulating fan capacity: 450000m3/h pressure:10000Pa motor power: 1800kW |
1 | 70 | |||
5 | Kiln inlet | high temperature fan capacity:480000m3/h pressure:7500Pa motor power: 1400kW |
104.2 | 1 | 85.00 |
water spray system 8000x30000 Volume: 480000m3/h Inlet air temp.: 350℃(max.450℃) Outlet air temp.: <150℃ Water-spraying volume: 2.0~20m3/h |
1 | 85.00 | |||
Bag filter capacity:480000m3/h outlet density: ≤30mg/Nm3 |
1 | 85.00 | |||
fan for waste gas capacity:480000m3/h pressure: 4000Pa motor power: 800kW |
1 | 85.00 | |||
5 cyclone pre-heater & pre-calciner system: RF5/2000 C1:2-Φ4600mm C2:1-Φ6500mm C3:1-Φ6500mm C4:1-Φ6800mm C5:1-Φ6800mm calciner:Φ5050x30000 mm Capacity:2500 t/d |
1 | 85.00 | |||
6 | Kiln | rotary kiln Type: Φ4.0×60m Slope: 4% rev 0.39-4.10r/min motor power:355kW(DC) |
104.2 | 1 | 85.00 |
7 | clinker cooling | grate cooler: third generation air beam type:LBT2500 grate effective area:65m2 discharge temperature: ambient temperature+65℃ Capacity:2500~3000 t/d |
104.2 | 1 | 85.00 |
8 | Kiln outlet waste gas treatment | heat exchanger processing volume: 300000m3/h inlet temperature : 250℃(max.450℃) outlet temperature: 130℃(max.180℃) |
1 | 85.00 | |
EP capacity:300000m3/h outlet density: ≤30mg/Nm3 |
1 | 85.00 | |||
blower for waste gas capacity:300000m3/h pressure:2300Pa motor power:355kW |
1 | 85.00 | |||
9 | cement grinding | cement mill Type: Ф3.8×13m feed grain size:≤25mm product fineness: specific area: 3400cm2/g motor power:2500kW |
70~75 | 2 | 75.00 |
separator N2000 type O-sepa Most feeding capacity:300t/h Product output:60~100t/h |
2 | 75.00 | |||
Bag filter Capacity: 120000m3/h Outlet density: ≤30mg/Nm3 |
2 | 75.00 | |||
Fan for waste gas Capacity: 12000m3/h Pressure: 8000Pa |
2 | 75.00 | |||
10 | Gypsum crushing |
Jaw crusher Type: PEX250×1000 maximum grain size: <210 mm discharge grain size :≤25 mm motor power: 37 kW |
20 | 1 | 20 |
11 | cement packing& bulk loading |
eight-mouthed rotary packing machine Weighing precision: +0.5kg -0.2kg |
100 | 2 | |
Bulk loading system | 150 | 3 | |||
12 | Air compressing station | screw air-boosting compressor discharge capacity: 23m3/min discharge pressure: 0.8MPa motor power: 132kW |
5 | 85.00 | |
Coal grinding | Ball mill Type: 3×(7+2)m Feed moisture: ≤10% Feed grain size: ≤25mm Discharge moisture: ≤1% Discharge fineness: 8-10%(0.08mm residue) Host motor power: 630kW |
20~22 | 1 | 68 | |
Coal mill dynamic separator Capacity: 16~20t/h Volume: 36000m3/h~50000m3/h Finess: ≤6%(0.08mm residue) Motor power: 22kW |
1 | 68 | |||
Bag filter Capacity: 55000m3/h outlet density: ≤30mg/Nm3 |
1 | 68 |
Quick Inquiry
Quick Inquiry