Publish Time:December 17, 2019
Cement production method
The production process of cement is simply two grinding and one sintering, that is, raw materials are mined, crushed, ground and mixed to produce raw materials. Raw materials are fired at 1450 ~ C high temperature to produce clinker. Clinker is crushed and ground together with gypsum or other mixed materials to become cement. Due to the difference between dry and wet raw meal preparation, the production methods are divided into three types: wet process, semi dry process or semi wet process and dry process.
幻灯片3
Characteristics of wet process production
The raw meal is made into slurry with water content of 32% - 36%, which is dried and fired into clinker in rotary kiln. Wet preparation of slurry, grinding energy consumption is low, about 30%, slurry is easy to mix, raw meal composition is stable, conducive to firing high quality clinker. The unit heat consumption of clinker in rotary kiln is 2093 ~ 2931kt / kg (500-700kcal / kg) higher than that of dry process kiln. The temperature of clinker discharged from the kiln is lower, so it is not suitable to burn clinker with high silica and high alumina content.
幻灯片4
Characteristics of semi dry production
Semi dry process is called semi dry process when dry raw meal powder is made by adding 10% ~ 15% water into kiln. Rotary kiln with grate heater is also called lipol kiln and shaft kiln are produced by semi dry process. In foreign countries, there is a kind of slurry prepared by wet method, which is pressed and dehydrated by mechanical method, and then made into mud section with water content of about 19%, and then calcined in lipol kiln, which is called semi wet process production. The moisture content of raw materials in semi dry process is reduced, and the unit heat consumption of clinker can also be reduced by 837 ~ 1675kj / kg (200 ~ 400kcal / kg) compared with that of wet process. Because the grate heater is used to replace part of the rotary kiln to dry the material ball, the rotary kiln can be shortened. For example, the unit volume output of the kiln can be increased by 2-3 times. However, the semi dry process requires that the raw meal should have a certain plasticity to form balls, so its application is limited to a certain extent. There are many mechanical failures in the heating machine. In China, the calcination temperature is generally low, so it is not suitable to burn high-quality clinker.
幻灯片5
Characteristics of dry production
In dry process, the raw meal powder is directly sent into the kiln for calcination, and the moisture content of the raw meal entering the kiln is generally only 1% ~ 2%, which saves a lot of heat needed for drying raw meal. In the past, hollow rotary kiln was used in dry process production, and the heat transfer efficiency in kiln was low, especially in decomposition zone with high heat consumption, so the thermal efficiency of dry process hollow kiln was not improved much. The raw meal powder prepared by dry method is not easy to mix evenly, which affects the quality of clinker. Therefore, wet process production was dominant in the 1940s-1950s. In the 1950s, the air stirring technology and suspension preheating technology of raw meal powder appeared. In the early 1970s, the pre decomposition technology, raw material pre homogenization and raw meal quality control technology were born. Now dry process production can completely prepare raw meal with uniform quality. The new precalciner kiln has moved the preheating of raw meal powder and decomposition of carbonate to the external suspension state of kiln, which has high thermal efficiency, reduces the load of rotary kiln, and not only reduces the heat consumption, but also increases the thermal efficiency of rotary kiln from 30% to 60% of wet kiln, and expands the production capacity of kiln.
幻灯片6
Main process flow of cement plant
The cement production process is mainly divided into three stages: raw material preparation, clinker burning and cement grinding.
Taking dry process production as an example, it includes the following main processes:
crushing and pre homogenizing raw meal- preparation raw meal homogenization -preheating decomposition cement clinker- firing cement grinding- cement packaging
幻灯片7
1.Crushing and pre homogenization
(1)In the production process of crushed cement, most raw materials need to be crushed, such as limestone, clay, iron ore and coal.
(2)Raw material pre homogenization technology is to use scientific stacking technology to realize the preliminary homogenization of raw materials in the process of storage and taking of raw materials, so that the raw material yard has the function of storage and homogenization at the same time.
幻灯片8
2.Raw meal preparation
In the process of cement production, at least 3 tons of materials (including various raw materials, fuel, clinker, mixture and gypsum) should be ground for each ton of Portland cement production. According to statistics, the power consumed by grinding of dry process cement production line accounts for more than 60% of the total power, in which raw material grinding accounts for more than 30%, coal mill accounts for about 3%, and cement grinding accounts for about 40%. Therefore, reasonable selection of grinding equipment and process flow, optimization of process parameters, correct operation and control of operation system are of great significance to ensure product quality and reduce energy consumption.
幻灯片9
3.Raw meal homogenization
In the production process of new dry process cement, stabilizing the composition of raw material into the pit is the premise of stabilizing the thermal system of clinker burning, and the homogenization system of raw meal plays the last key role in stabilizing the composition of raw material entering the pit.
幻灯片10
4.Preheat decomposition
The preheating and partial decomposition of raw meal are completed by preheater instead of part of rotary kiln function, so as to shorten the length of return kiln, at the same time, the heat exchange process of gas in the kiln is carried out in the state of internal suspension of preheater, so that the raw meal can be fully mixed with the hot gas discharged from the kiln, thus increasing the contact area of gas and material, fast heat transfer speed and high heat exchange efficiency To improve the production efficiency of kiln system and reduce the heat consumption of clinker.
(1) Material dispersion (2) gas solid separation (3) pre decomposition
幻灯片11
5.Sintering of cement clinker
After the raw meal is preheated and pre decomposed in the cyclone preheater, the next process is to enter the rotary kiln for clinker burning.
In the rotary kiln, the carbonate is further decomposed rapidly and a series of solid-state reactions take place, resulting in the formation of other minerals in cement clinker. With the increase of material temperature, some minerals will become liquid phase and dissolve in liquid phase to produce a large amount of clinker. After the clinker is fired, the temperature begins to decrease. Finally, the cement clinker cooler cools the high temperature clinker discharged from the rotary kiln to the temperature that the downstream transportation, storage and cement grinding can bear. At the same time, the sensible heat of high-temperature clinker is recovered to improve the thermal efficiency and clinker quality of the system.
幻灯片12
6.Cement grinding
Cement grinding is the final process of cement production line manufacturing, and also the most power consuming process. Its main function is to grind the cement clinker (and gelling agent, performance regulating material, etc.) to the appropriate particle size (expressed by fineness, specific surface area, etc.), form a certain particle gradation, increase its hydration area, accelerate the hydration speed, and meet the requirements of setting and hardening of cement paste.
幻灯片13
7.Cement packing
There are two ways of cement delivery, bagged and bulk.
幻灯片14
Cement production equipment
1.Cement kiln system
Cement kiln is the main equipment of cement plant. The whole process of burning clinker from raw material is completed in the kiln. The simplest rotary kiln is dry hollow kiln. The raw material powder is added from the kiln tail, and the pulverized coal is injected from the kiln head with primary air and burned in the kiln. The flame temperature here reaches 1800-2000 ℃. The raw material continuously flows to the kiln head in the kiln, and the humidity gradually increases. After drying, dehydration, preheating and decomposition, the liquid phase appears when it reaches about 1300 ° C, then it rises to 1450 ° C under the flame, and then it cools to 1300 ~ 1100 ℃ to leave the rotary kiln and fall into the single barrel cooler. When it is cooled to about 100-150 ℃, it is unloaded to the clinker conveyor and transported to the clinker crusher, and then stored in storage after crushing.
幻灯片15
2.Rotary kiln system
The rotary kiln is a cylinder made of steel plate and lined with refractory bricks. It is supported by the wheel belt on the loading shell and the supporting wheel below. It is driven by the big gear ring installed on the kiln body. The rotary kiln is usually placed at a slope of 3.5%, the speed is generally within 1 rpm, and the new dry process kiln can reach more than 3 rpm. The single drum cooler is similar to the kiln in that it is equipped with a lifting plate to speed up the clinker cooling. The temperature of the cylinder in the high temperature zone of kiln head is too high. It was cooled by water before, but now it is cooled by air. the above-mentioned dry process hollow kiln is the basic kiln type. Other kiln types mainly change the structure and type of drying, preheating and decomposition parts at the rear, and change the clinker cooler.
幻灯片16
3.Cement grinding station
If the process of cement production equipment is regarded as a complete process system, the final product is cement and the clinker is semi-finished product. Therefore, the system can be separated. The process from raw material excavation to clinker production is one stage, and the second stage is cement made from clinker and shipment and delivery. In general, these two sections should be put together, so as to occupy less land, facilitate management, use less labor, and can be completely centralized control. However, in some special cases, separation is more advantageous.
幻灯片17
4.Grinding system
Ball mill is the earliest grinding equipment used in cement production industry, and it still plays a leading role. Although its efficiency is very low, for example, the power consumption of single particle is only 6% - 9%, the maintenance of ball mill is simple and reliable, especially for cement clinker grinding. The shape and gradation of product particles are appropriate, and the performance of cement is good. It is difficult to find equipment that can completely replace it.
幻灯片18
一:Raw meal preparation
l 1.Limestone plate feeder
l It is located in limestone crushing workshop
l Application for limestone feeding
l 2.Limestone crusher
l It is used for crushing limestone
l It is located in limestone crushing workshop of the plant
l Crushing type single stage hammer type (pcf20.18)
l 3.Limestone blending stacker reclaimer
幻灯片19
二:Raw material grinding
Ball mill
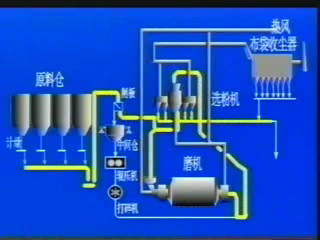
幻灯片20
Vertical mill

幻灯片21
4. Roller mill
5.Bag dust collector at kiln tail
Specification and model outdoor type
It is used for collecting raw material powder from waste gas of kiln tail and raw material mill
It is located behind the humidifier tower and raw material mill
6.Exhaust fan of bag dust collector at kiln tail
Application for waste gas treatment of kiln tail and raw material mill system The layout is located after the bag dust collection at the kiln tail
Normal working air temperature: 80 ~ 150 ℃, limit temperature: 200 ℃
7.High temperature fan at kiln tail
It is used to extract exhaust gas from preheater
The layout is located behind the preheater and the humidification tower Normal temperature of working air temperature: 320 ~ 350 ℃;
Limit temperature: 450 ℃;
Fan blades should be made of high-quality wear-resistant materials to ensure long service life of rotor blades.
8.Circulating fan of raw material mill
Used for ventilation of raw material mill system
The arrangement position is behind the combined cyclone of raw material mill
Normal working air temperature: 90 ~ 100 ℃ limit temperature (short time): 250 ℃
Fan blades should be made of high-quality wear-resistant materials to ensure long service life of rotor blades.
幻灯片22
三:Clinker firing
Calciner
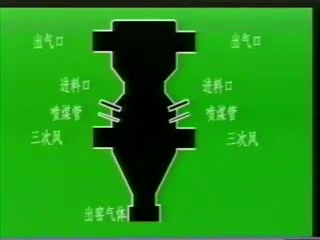
幻灯片23
Preheater
The preheating and partial decomposition of raw meal are completed by preheater instead of part of rotary kiln function, so as to shorten the length of return kiln, at the same time, the heat exchange process of gas in the kiln is carried out in the state of internal suspension of preheater, so that the raw meal can be fully mixed with the hot gas discharged from the kiln, thus increasing the contact area of gas and material, fast heat transfer speed and high heat exchange efficiency To improve the production efficiency of kiln system and reduce the heat consumption of clinker.
幻灯片24
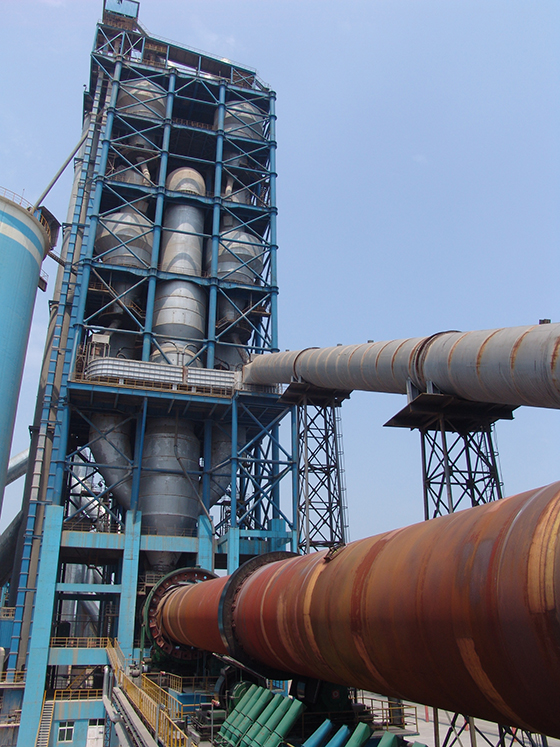
幻灯片25
9.Storage bucket elevator
Usage: raw material storage (outdoor type with head maintenance platform)
10.Kiln feeding bucket elevator
Purpose raw material into preheater (outdoor type with head maintenance platform)
11.Rotary kiln
12. Grate Cooler
13.Grate cooler cooling fan
Purpose and location: it is used to supply air for exhaust gas of grate cooler, which is arranged around grate cooler
14.Electric dust collector at kiln head
It is used for residual air treatment of grate cooler at kiln head
The layout is located behind the cooler and in front of the electric dust collector and exhaust fan at the kiln head
15.Electric dust collector and exhaust fan at kiln head
It is used to drain the waste gas of cooling machine after purification by electric dust collector
The layout is located behind the kiln head cooler and electric dust collector
Normal working air temperature: 200 ~ 250 ℃, maximum (short time): 400 ℃
Fan blades should be made of high-quality wear-resistant materials to ensure long service life of rotor blades.
16. Clinker chain bucket conveyor
幻灯片26
四:Cement grinding
17Cement grinding station
18Separator

The production process of cement is simply two grinding and one sintering, that is, raw materials are mined, crushed, ground and mixed to produce raw materials. Raw materials are fired at 1450 ~ C high temperature to produce clinker. Clinker is crushed and ground together with gypsum or other mixed materials to become cement. Due to the difference between dry and wet raw meal preparation, the production methods are divided into three types: wet process, semi dry process or semi wet process and dry process.
幻灯片3
Characteristics of wet process production
The raw meal is made into slurry with water content of 32% - 36%, which is dried and fired into clinker in rotary kiln. Wet preparation of slurry, grinding energy consumption is low, about 30%, slurry is easy to mix, raw meal composition is stable, conducive to firing high quality clinker. The unit heat consumption of clinker in rotary kiln is 2093 ~ 2931kt / kg (500-700kcal / kg) higher than that of dry process kiln. The temperature of clinker discharged from the kiln is lower, so it is not suitable to burn clinker with high silica and high alumina content.
幻灯片4
Characteristics of semi dry production
Semi dry process is called semi dry process when dry raw meal powder is made by adding 10% ~ 15% water into kiln. Rotary kiln with grate heater is also called lipol kiln and shaft kiln are produced by semi dry process. In foreign countries, there is a kind of slurry prepared by wet method, which is pressed and dehydrated by mechanical method, and then made into mud section with water content of about 19%, and then calcined in lipol kiln, which is called semi wet process production. The moisture content of raw materials in semi dry process is reduced, and the unit heat consumption of clinker can also be reduced by 837 ~ 1675kj / kg (200 ~ 400kcal / kg) compared with that of wet process. Because the grate heater is used to replace part of the rotary kiln to dry the material ball, the rotary kiln can be shortened. For example, the unit volume output of the kiln can be increased by 2-3 times. However, the semi dry process requires that the raw meal should have a certain plasticity to form balls, so its application is limited to a certain extent. There are many mechanical failures in the heating machine. In China, the calcination temperature is generally low, so it is not suitable to burn high-quality clinker.
幻灯片5
Characteristics of dry production
In dry process, the raw meal powder is directly sent into the kiln for calcination, and the moisture content of the raw meal entering the kiln is generally only 1% ~ 2%, which saves a lot of heat needed for drying raw meal. In the past, hollow rotary kiln was used in dry process production, and the heat transfer efficiency in kiln was low, especially in decomposition zone with high heat consumption, so the thermal efficiency of dry process hollow kiln was not improved much. The raw meal powder prepared by dry method is not easy to mix evenly, which affects the quality of clinker. Therefore, wet process production was dominant in the 1940s-1950s. In the 1950s, the air stirring technology and suspension preheating technology of raw meal powder appeared. In the early 1970s, the pre decomposition technology, raw material pre homogenization and raw meal quality control technology were born. Now dry process production can completely prepare raw meal with uniform quality. The new precalciner kiln has moved the preheating of raw meal powder and decomposition of carbonate to the external suspension state of kiln, which has high thermal efficiency, reduces the load of rotary kiln, and not only reduces the heat consumption, but also increases the thermal efficiency of rotary kiln from 30% to 60% of wet kiln, and expands the production capacity of kiln.
幻灯片6
Main process flow of cement plant
The cement production process is mainly divided into three stages: raw material preparation, clinker burning and cement grinding.
Taking dry process production as an example, it includes the following main processes:
crushing and pre homogenizing raw meal- preparation raw meal homogenization -preheating decomposition cement clinker- firing cement grinding- cement packaging
幻灯片7
1.Crushing and pre homogenization
(1)In the production process of crushed cement, most raw materials need to be crushed, such as limestone, clay, iron ore and coal.
(2)Raw material pre homogenization technology is to use scientific stacking technology to realize the preliminary homogenization of raw materials in the process of storage and taking of raw materials, so that the raw material yard has the function of storage and homogenization at the same time.
幻灯片8
2.Raw meal preparation
In the process of cement production, at least 3 tons of materials (including various raw materials, fuel, clinker, mixture and gypsum) should be ground for each ton of Portland cement production. According to statistics, the power consumed by grinding of dry process cement production line accounts for more than 60% of the total power, in which raw material grinding accounts for more than 30%, coal mill accounts for about 3%, and cement grinding accounts for about 40%. Therefore, reasonable selection of grinding equipment and process flow, optimization of process parameters, correct operation and control of operation system are of great significance to ensure product quality and reduce energy consumption.
幻灯片9
3.Raw meal homogenization
In the production process of new dry process cement, stabilizing the composition of raw material into the pit is the premise of stabilizing the thermal system of clinker burning, and the homogenization system of raw meal plays the last key role in stabilizing the composition of raw material entering the pit.
幻灯片10
4.Preheat decomposition
The preheating and partial decomposition of raw meal are completed by preheater instead of part of rotary kiln function, so as to shorten the length of return kiln, at the same time, the heat exchange process of gas in the kiln is carried out in the state of internal suspension of preheater, so that the raw meal can be fully mixed with the hot gas discharged from the kiln, thus increasing the contact area of gas and material, fast heat transfer speed and high heat exchange efficiency To improve the production efficiency of kiln system and reduce the heat consumption of clinker.
(1) Material dispersion (2) gas solid separation (3) pre decomposition
幻灯片11
5.Sintering of cement clinker
After the raw meal is preheated and pre decomposed in the cyclone preheater, the next process is to enter the rotary kiln for clinker burning.
In the rotary kiln, the carbonate is further decomposed rapidly and a series of solid-state reactions take place, resulting in the formation of other minerals in cement clinker. With the increase of material temperature, some minerals will become liquid phase and dissolve in liquid phase to produce a large amount of clinker. After the clinker is fired, the temperature begins to decrease. Finally, the cement clinker cooler cools the high temperature clinker discharged from the rotary kiln to the temperature that the downstream transportation, storage and cement grinding can bear. At the same time, the sensible heat of high-temperature clinker is recovered to improve the thermal efficiency and clinker quality of the system.
幻灯片12
6.Cement grinding
Cement grinding is the final process of cement production line manufacturing, and also the most power consuming process. Its main function is to grind the cement clinker (and gelling agent, performance regulating material, etc.) to the appropriate particle size (expressed by fineness, specific surface area, etc.), form a certain particle gradation, increase its hydration area, accelerate the hydration speed, and meet the requirements of setting and hardening of cement paste.
幻灯片13
7.Cement packing
There are two ways of cement delivery, bagged and bulk.
幻灯片14
Cement production equipment
1.Cement kiln system
Cement kiln is the main equipment of cement plant. The whole process of burning clinker from raw material is completed in the kiln. The simplest rotary kiln is dry hollow kiln. The raw material powder is added from the kiln tail, and the pulverized coal is injected from the kiln head with primary air and burned in the kiln. The flame temperature here reaches 1800-2000 ℃. The raw material continuously flows to the kiln head in the kiln, and the humidity gradually increases. After drying, dehydration, preheating and decomposition, the liquid phase appears when it reaches about 1300 ° C, then it rises to 1450 ° C under the flame, and then it cools to 1300 ~ 1100 ℃ to leave the rotary kiln and fall into the single barrel cooler. When it is cooled to about 100-150 ℃, it is unloaded to the clinker conveyor and transported to the clinker crusher, and then stored in storage after crushing.
幻灯片15
2.Rotary kiln system
The rotary kiln is a cylinder made of steel plate and lined with refractory bricks. It is supported by the wheel belt on the loading shell and the supporting wheel below. It is driven by the big gear ring installed on the kiln body. The rotary kiln is usually placed at a slope of 3.5%, the speed is generally within 1 rpm, and the new dry process kiln can reach more than 3 rpm. The single drum cooler is similar to the kiln in that it is equipped with a lifting plate to speed up the clinker cooling. The temperature of the cylinder in the high temperature zone of kiln head is too high. It was cooled by water before, but now it is cooled by air. the above-mentioned dry process hollow kiln is the basic kiln type. Other kiln types mainly change the structure and type of drying, preheating and decomposition parts at the rear, and change the clinker cooler.
幻灯片16
3.Cement grinding station
If the process of cement production equipment is regarded as a complete process system, the final product is cement and the clinker is semi-finished product. Therefore, the system can be separated. The process from raw material excavation to clinker production is one stage, and the second stage is cement made from clinker and shipment and delivery. In general, these two sections should be put together, so as to occupy less land, facilitate management, use less labor, and can be completely centralized control. However, in some special cases, separation is more advantageous.
幻灯片17
4.Grinding system
Ball mill is the earliest grinding equipment used in cement production industry, and it still plays a leading role. Although its efficiency is very low, for example, the power consumption of single particle is only 6% - 9%, the maintenance of ball mill is simple and reliable, especially for cement clinker grinding. The shape and gradation of product particles are appropriate, and the performance of cement is good. It is difficult to find equipment that can completely replace it.
幻灯片18
一:Raw meal preparation
l 1.Limestone plate feeder
l It is located in limestone crushing workshop
l Application for limestone feeding
l 2.Limestone crusher
l It is used for crushing limestone
l It is located in limestone crushing workshop of the plant
l Crushing type single stage hammer type (pcf20.18)
l 3.Limestone blending stacker reclaimer
幻灯片19
二:Raw material grinding
Ball mill
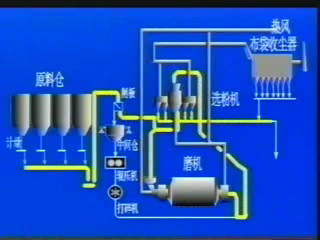
幻灯片20
Vertical mill

幻灯片21
4. Roller mill
5.Bag dust collector at kiln tail
Specification and model outdoor type
It is used for collecting raw material powder from waste gas of kiln tail and raw material mill
It is located behind the humidifier tower and raw material mill
6.Exhaust fan of bag dust collector at kiln tail
Application for waste gas treatment of kiln tail and raw material mill system The layout is located after the bag dust collection at the kiln tail
Normal working air temperature: 80 ~ 150 ℃, limit temperature: 200 ℃
7.High temperature fan at kiln tail
It is used to extract exhaust gas from preheater
The layout is located behind the preheater and the humidification tower Normal temperature of working air temperature: 320 ~ 350 ℃;
Limit temperature: 450 ℃;
Fan blades should be made of high-quality wear-resistant materials to ensure long service life of rotor blades.
8.Circulating fan of raw material mill
Used for ventilation of raw material mill system
The arrangement position is behind the combined cyclone of raw material mill
Normal working air temperature: 90 ~ 100 ℃ limit temperature (short time): 250 ℃
Fan blades should be made of high-quality wear-resistant materials to ensure long service life of rotor blades.
幻灯片22
三:Clinker firing
Calciner
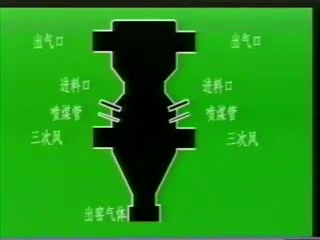
幻灯片23
Preheater
The preheating and partial decomposition of raw meal are completed by preheater instead of part of rotary kiln function, so as to shorten the length of return kiln, at the same time, the heat exchange process of gas in the kiln is carried out in the state of internal suspension of preheater, so that the raw meal can be fully mixed with the hot gas discharged from the kiln, thus increasing the contact area of gas and material, fast heat transfer speed and high heat exchange efficiency To improve the production efficiency of kiln system and reduce the heat consumption of clinker.
幻灯片24
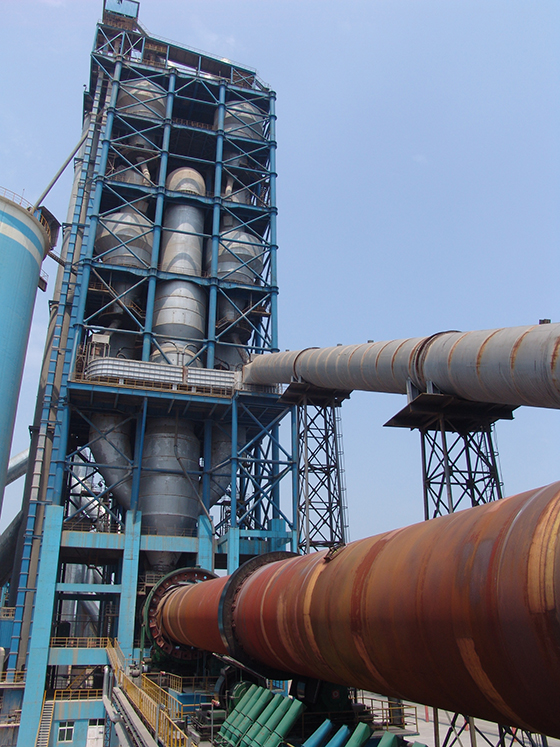
幻灯片25
9.Storage bucket elevator
Usage: raw material storage (outdoor type with head maintenance platform)
10.Kiln feeding bucket elevator
Purpose raw material into preheater (outdoor type with head maintenance platform)
11.Rotary kiln
12. Grate Cooler
13.Grate cooler cooling fan
Purpose and location: it is used to supply air for exhaust gas of grate cooler, which is arranged around grate cooler
14.Electric dust collector at kiln head
It is used for residual air treatment of grate cooler at kiln head
The layout is located behind the cooler and in front of the electric dust collector and exhaust fan at the kiln head
15.Electric dust collector and exhaust fan at kiln head
It is used to drain the waste gas of cooling machine after purification by electric dust collector
The layout is located behind the kiln head cooler and electric dust collector
Normal working air temperature: 200 ~ 250 ℃, maximum (short time): 400 ℃
Fan blades should be made of high-quality wear-resistant materials to ensure long service life of rotor blades.
16. Clinker chain bucket conveyor
幻灯片26
四:Cement grinding
17Cement grinding station
18Separator

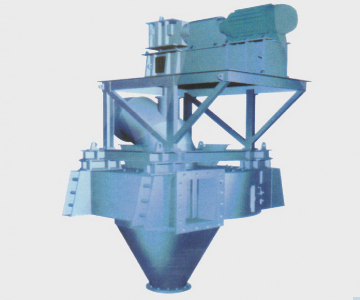