1500t / d cement production line
Pengfei EPC cement production line project includes process design, equipment supply (including mechanical and electrical parts), civil engineering, installation and commissioning, trial operation, reaching the production standard and final delivery and other services. Mechanical equipment includes limestone crushing and conveying, clay crushing, raw coal crushing, raw coal and auxiliary raw material pre homogenization yard, raw material proportioning station, raw material grinding and waste gas treatment, raw material homogenization silo and raw material feeding into kiln, firing kiln tail, firing kiln middle and tertiary air pipe, firing kiln head.
Introduction
Pengfei EPC cement production line project includes process design, equipment supply (including mechanical and electrical parts), civil engineering, installation and commissioning, trial operation, reaching the production standard and final delivery and other services. Mechanical equipment includes limestone crushing and conveying, clay crushing, raw coal crushing, raw coal and auxiliary raw material pre homogenization yard, raw material proportioning station, raw material grinding and waste gas treatment, raw material homogenization silo and raw material feeding into kiln, firing kiln tail, firing kiln middle and tertiary air pipe, firing kiln head, clinker conveying, clinker storage and conveying, pulverized coal preparation and metering conveying, cement proportioning station and clinker Bulk, gypsum, mixture crushing and conveying, cement grinding and conveying, cement storage and conveying, cement packaging, bagged cement loading, cement truck bulk, machine repair workshop and total material warehouse.Process parameters
(1) Clinker output: ≥ 1500 t / d;(2) heat consumption: ≥ 840kcal / kg clinker
(3) power consumption: ≥ 110kwh / t cement
(4) water consumption: maximum 1020m3/d
Production process
(1)Limestone & sandstone crushingThe limestone and sandstone are separately crushed by their respective crusher; There are discharged via belt conveyors. The two crushers are located at plant site.
(2) Limestone prehomogenizing and handling
The crushed limestone is stacked in the prehomogenizing hall.
The prehomogenized limestone is retrieved by a reclaimer and transported to raw mill feed bin by belt conveyor.
(3) Sandstone storage and handling
The sandstone is stored in the sandstone storage silo after being crushed. It is extracted from the storage silo by a belt extractor and transported to the raw mill feed bin by belt conveyor.
(4) Clay storage and handling
The clay is transported during dry season, from the clay quarry to the clay storage hall by trucks and stacked by either dozer or loader. From the storage hall, the clay is retrieved by loader and fed into a hopper and transported to the raw mill feed bin by belt conveyor.
The clay bin is equipped with a live bottom to prevent hang-ups and/or bridging of the material at discharge unto weighfeeder.
(5) Raw meal grinding and transport
The raw materials are extracted from their respective feed bins by belt type weighfeeders (apron type for clay) and transported by belt conveyor into raw mill system. The raw mill is a closed circuit air swept ball mill.
The raw meal product is transported into blending silo by air slide and bucket elevator.
The hot gas out of preheater is used as the heat source for drying in raw mill. There is also a standby oil furnace for supplying the hot gas when the kiln stops or the hot gas from preheater is not enough.
(6) Raw meal homogenizing and feeding into preheater
In the blending silo the raw meal is homogenized to achieve desired level of product consistency. From the blending silo the homogenized raw meal is fed into the preheater via the kiln feed system which consist of level box, flow valve, weight meter, airslide and bucket elevator,etc….
Technical
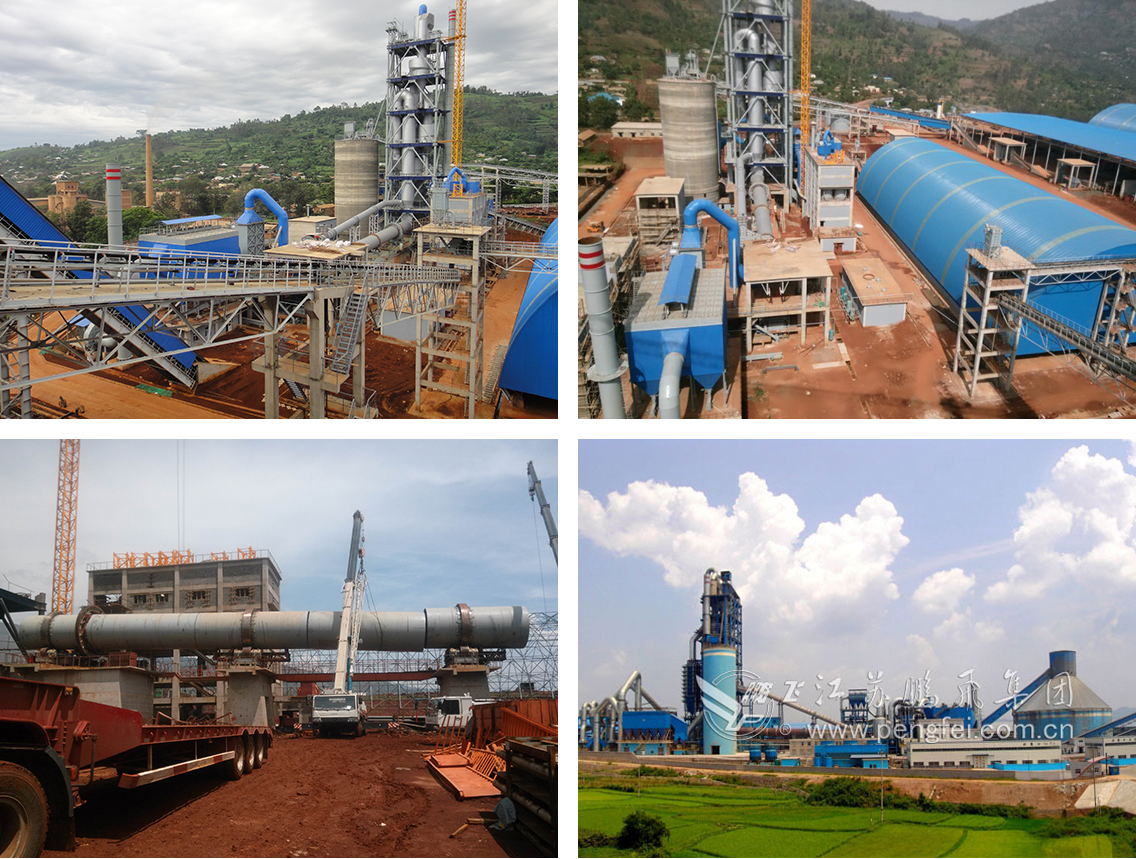
No. | Name of Workshop | Main Equipment | Working Programme (d/w×h/d) |
Qty |
1 | Limestone | Single hammer crusher Feed size:≤800×800×1000mm Crushing system capacity: 350 t/h Product size:90% ≤25mm |
6d/w×7h/d | 1 |
2 | Sandstone crushing and conveying | High efficiency crusher Feed size:≤215 mm Crushing system capacity: 50 t/h Product size:90% ≤20 mm |
1d/w×7h/d | |
3 | Limestone prehomogenizing and conveying | Stacker Capacity:350 t/h |
6d/w×7h/d | 1 |
Reclaimer Capacity:150 t/h |
7d/w×20h/d | 1 | ||
4 | Raw peat Prehomogenizing and conveying |
Feed hopper with extractor Peat extractor: 80 t/h Peat conveying: 30 t/h |
7d/w×4h/d | 1 |
5 | Raw material grinding | Closed circuit Ball mill Φ 4.0X9 m (precrushing /drying) Feed size:≤25mm Product fineness: <R12% @ 80 μ Feed moisture:≤ 8% Product moisture: <1% Capacity: 120 t/h |
7d/w×20h/d | 1 |
6 | Peat grinding | Closed circuit ball mill Φ 2.6x(5.25+2.25)m Feed size: ≤25mm Product fineness: <R 10% @ 80μ Feed moisture:max.12% Product moisture: <1.5% Capacity: 13-15 t/h |
6d/w×20h/d | 1 |
7 | Clinker burning Temperature @ cyclones outlet ≤350±10°C |
Five-stage cyclones, Preheater + precalciner: C1:2-Φ5450 mm C2:1-Φ5450 mm C3:1-Φ5450 mm C4:1-Φ5700 mm C5:1-Φ5700 mm Precalciner:1- Φ 4600 mm Temperature @ cyclones outlet ≤350±10°C Rotary kiln : Φ3.5X54m Heat consumption: ≤840kcal/kg Capacity: 1500t/d (62.5t/h) Power:220 kW, DC Fuel: Fuel oil and peat Grate cooler: mechanical drive Bed area: 39 m2 Capacity:1500t/d |
7d/w×24h/d | 1 |
8 | Cement grinding | Ball mill: Two closed circuit Φ3.2×13m. Product size: <R3.5% @ 80μ Capacity: 2×50 t/h PC32.5 Power: 2 × 1600 kW |
7d/w×22h/d | 2 |
9 | Cement bagging | Two 8 spouts rotating packers Capacity:2x100 t/h One bulky station provided. |
6d/w×12h/d | 2 |
Quick Inquiry
Quick Inquiry